Guía del hormigón
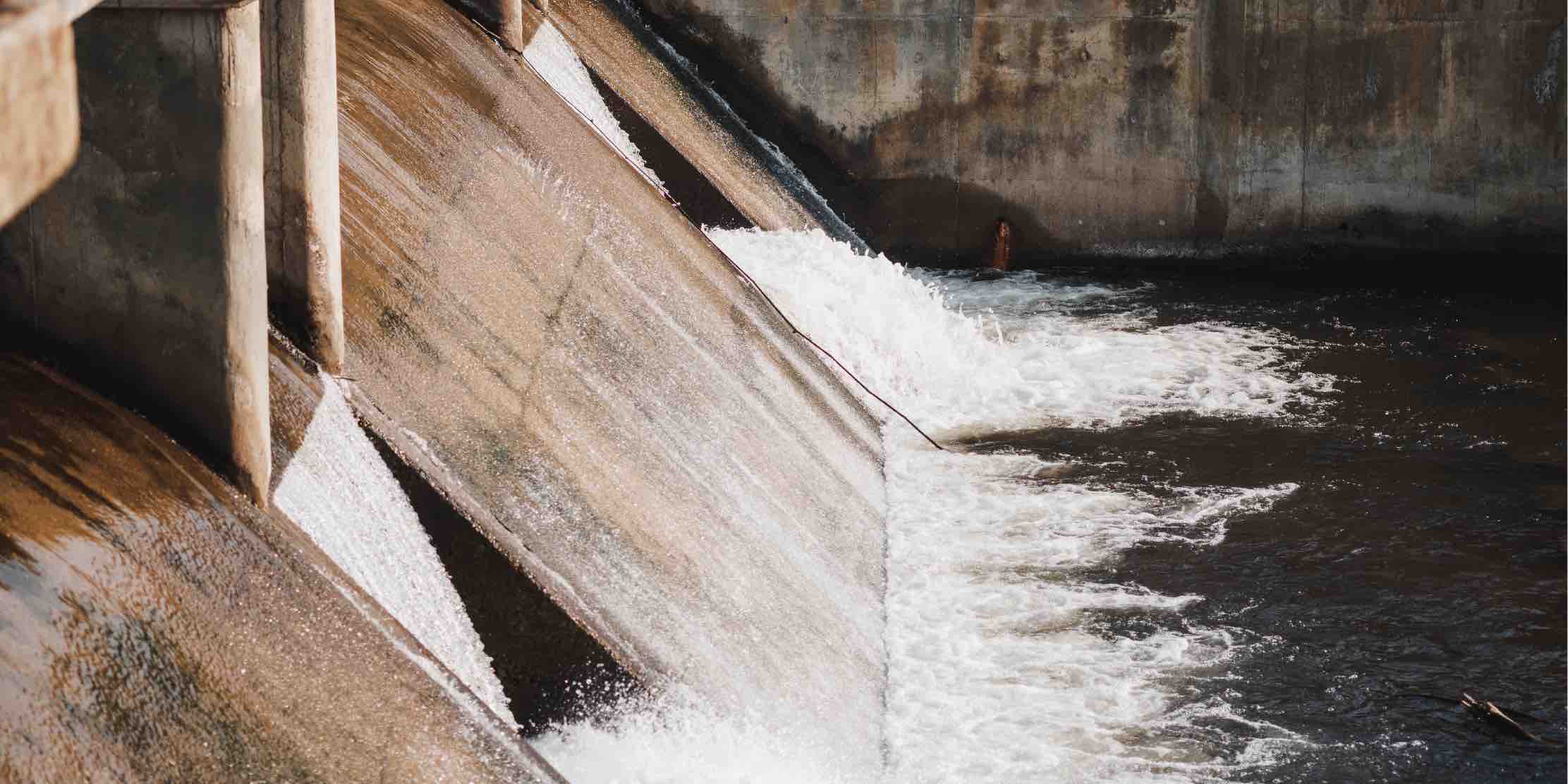
Tipologías de hormigón
Te mostramos una clasificación de las tipologías de hormigón más habituales:
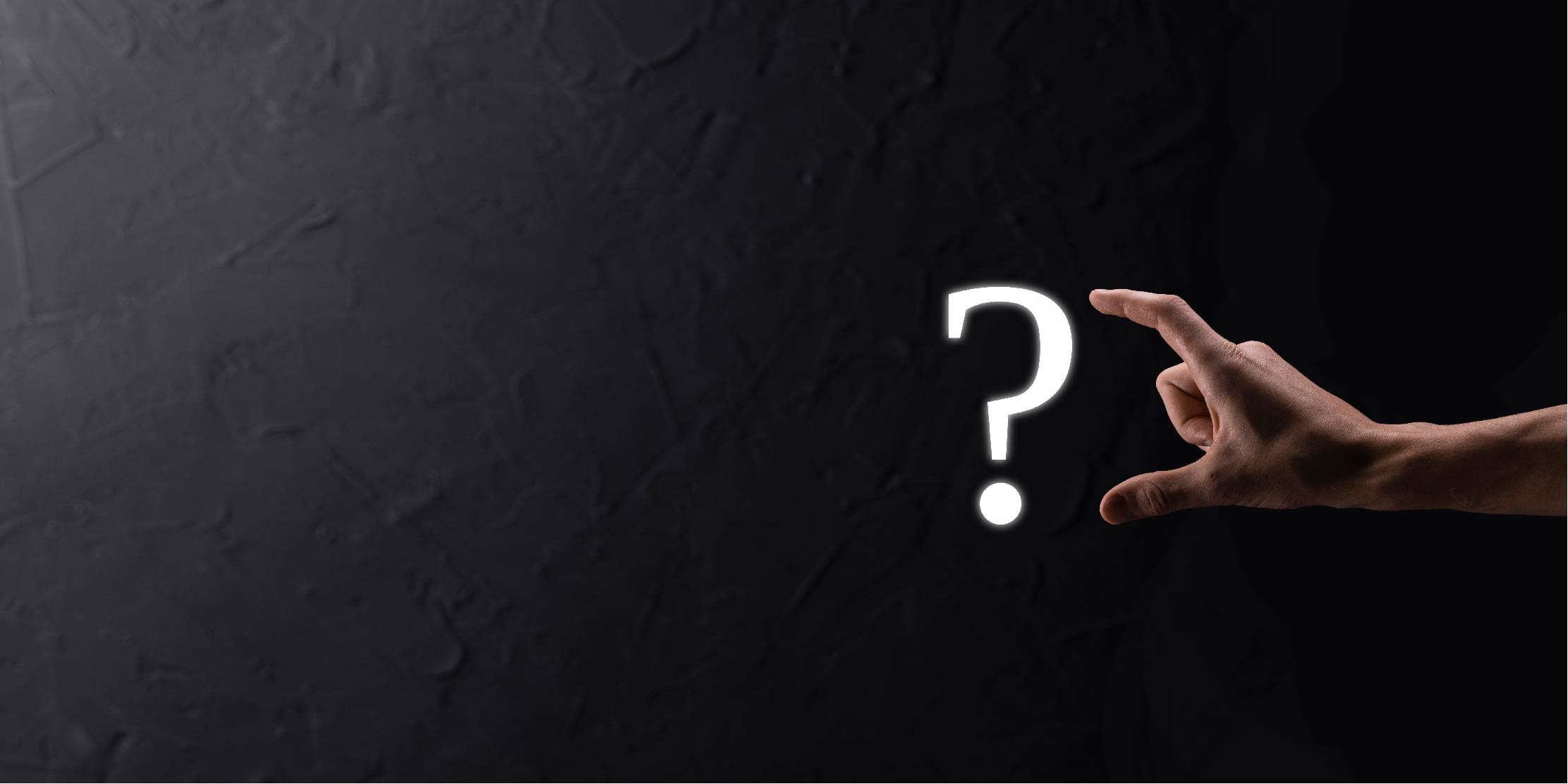
Respuestas al hormigón
- Cómo medir la dureza del hormigón
- Cuánto tarda en fraguar el hormigón
- Qué pasa si llueve sobre el hormigón fresco
- Cómo de resistente es el hormigón ante el fuego
- Qué es el hormigón C40
- Qué es el hormigón C25
- Por qué el hormigón lleva arena
- Cuál es la razón de la aparición de grietas de retracción en el hormigón fresco
- Qué durabilidad tiene el hormigón
- Por qué se levanta el hormigon
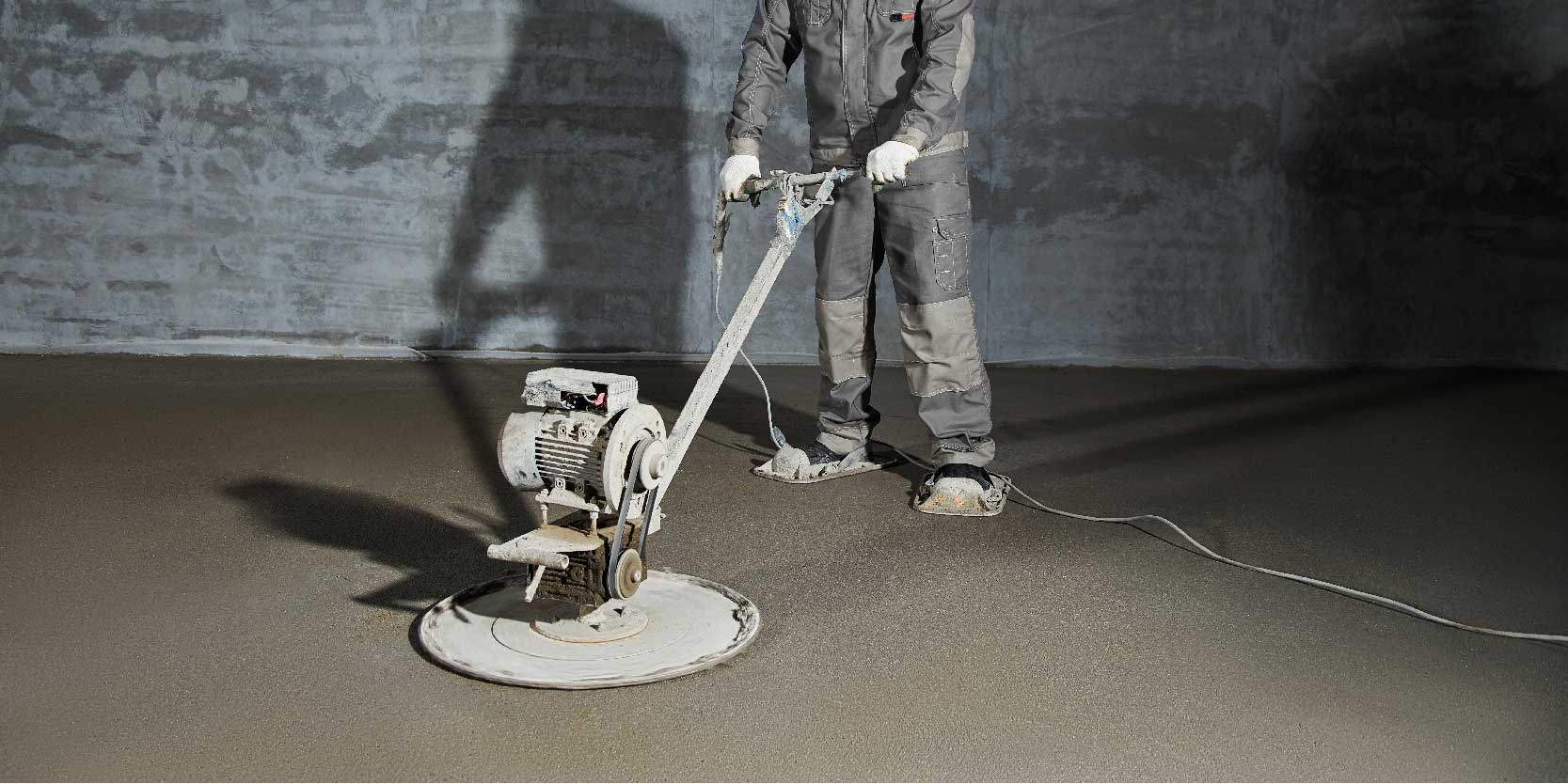
Acabados del hormigón
Tras mucha innovación, hoy en día el mercado ofrece una extensa gama de acabados que te mostramos aquí:
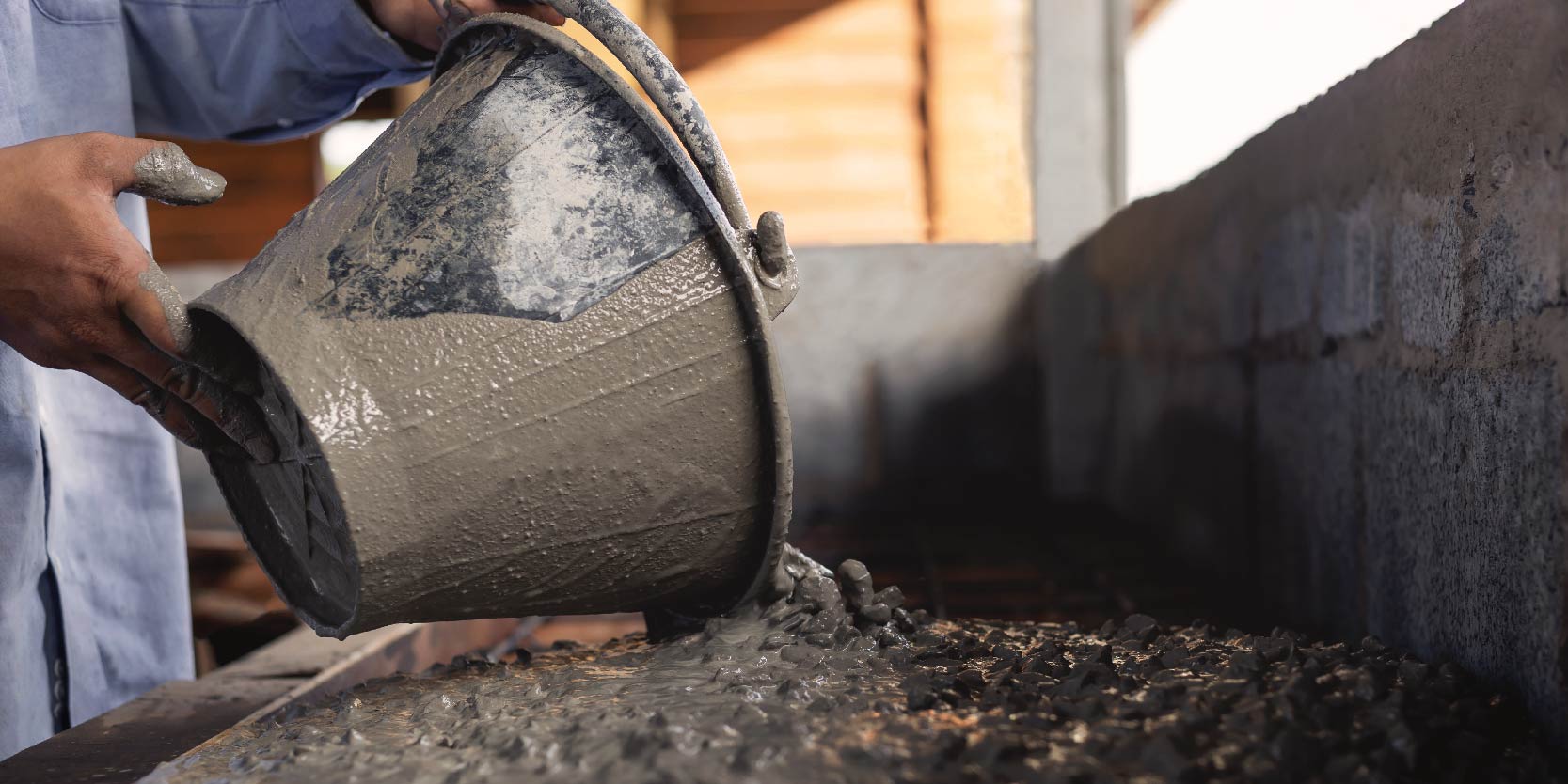
Según su estado
Desde su producción hasta llegar a su estado sólido, el hormigón pasa principalmente por 2 etapas:
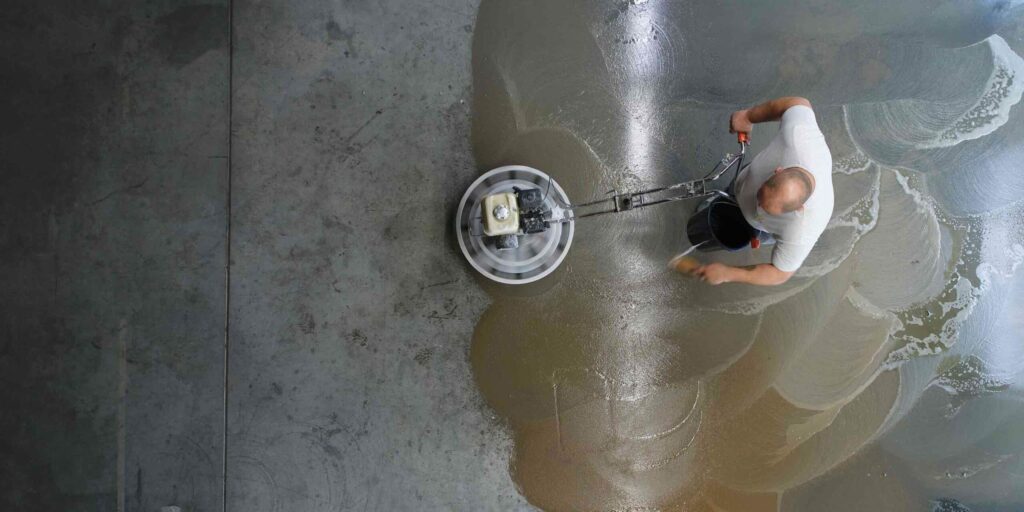
Fortaleciendo al hormigón
El hormigón puede ser fortalecido aun más a través de una serie de tratamientos: