Los morteros autonivelantes hacen referencia a un tipo de mortero que es usado como base para suelos vinílicos, tarimas flotantes, suelo laminado, y baldosas.
Estos forman parte del grupo especial de morteros según la norma DIN 18550, también llamados morteros Justacken, los cuales presentan en su composición, a una serie de aditivos que se ocupan de atribuirle unas cualidades sobresalientes y diferentes del resto.
What is a self-leveling mortar?
Este es un mortero especial, el cual destaca por ser sumamente líquido. Su composición no difiere demasiado respecto al resto de los morteros especiales, puesto que consisten en la unión de cemento o anhidrita y arena granulométricamente fina. La diferencia se manifiesta en que este logra un acabado más liso y nivelado debido a su fluidez.
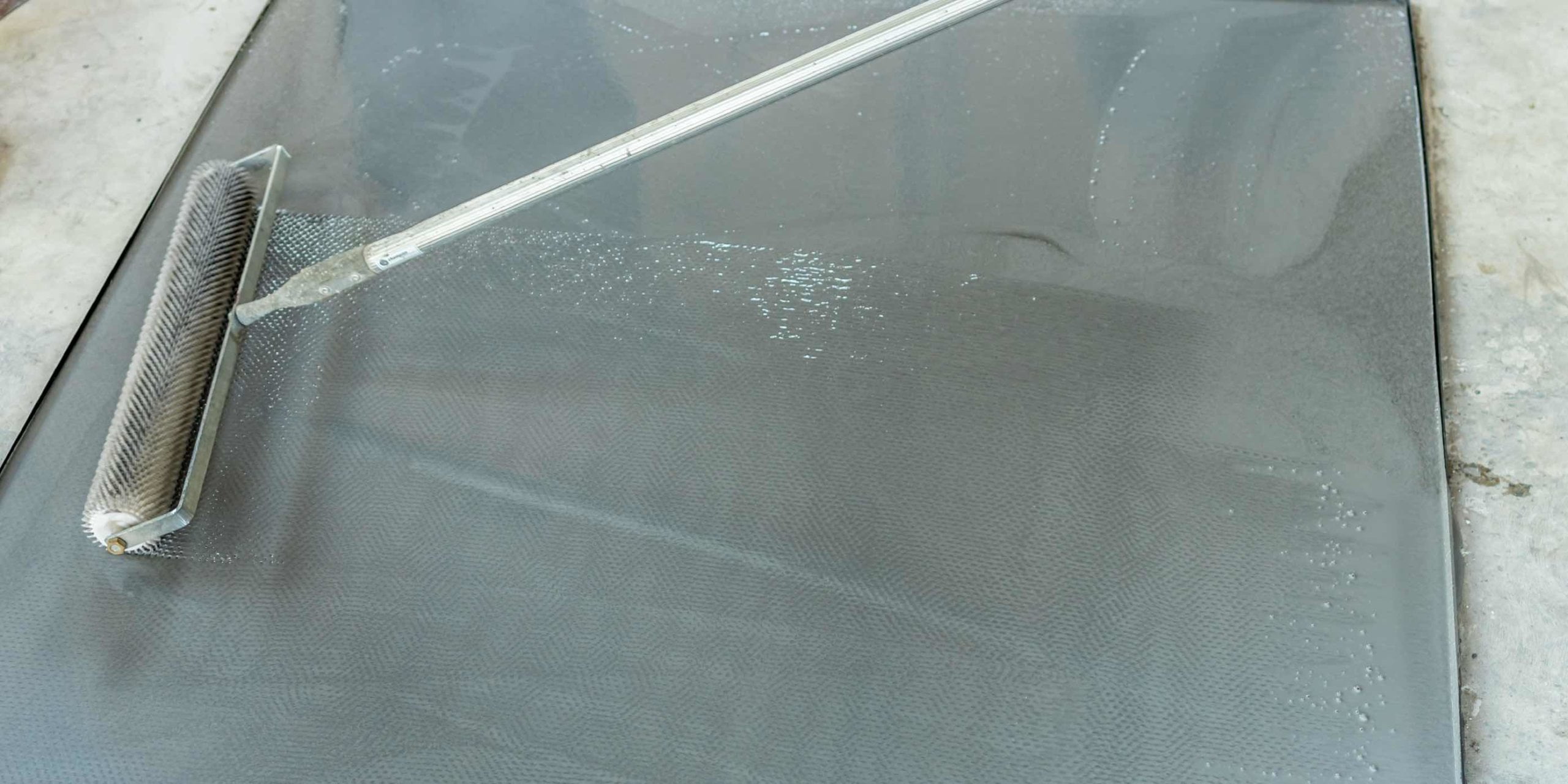
Aditivos empleados
The most commonly used additives to create self-leveling mortar are the following:
- Superfluidifiers, causing its characteristic liquid consistency.
- Retraction reducers, essential to control retraction due to excess water in the mix.
- Air entrainers, improving plasticity and reducing the density of the mixture.
- Viscosity modifiers, preventing aggregates from falling to the bottom.
The adverse consequence of using these additives is the mortar’s resistance reduction, being lower than conventional mixes.
It is fair to say that the name of this mortar is inaccurate since it requires manual smoothing to provide surface regularity, lacking mechanical self-sufficiency.
Composition details
Anhydrite is a mineral that has recently gained ecological relevance, since it has been used as a substitute for Portland cement due to its low pollutant emissions, presenting interesting and positive results in many constructive aspects.
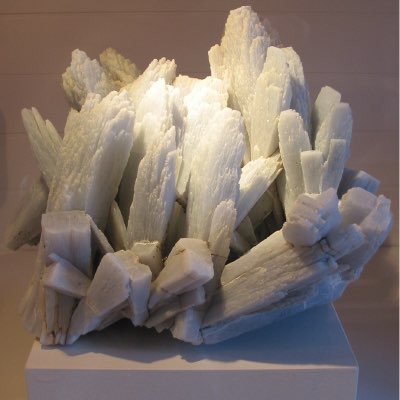
Las bondades principales de la anhidrita como conglomerante de morteros son la generación de espesores mínimos de 2,5 cm y una gran conductividad térmica. Además, conserva las cualidades fisicoquímicas para la nivelación de la superficie.
Anhydrite is obtained from the residues of the fluorine industry, in the form of calcium sulfate, which must be properly subjected to a series of chemical reactions to isolate the precious mineral.
Uses of self-leveling mortar
El objetivo primordial de un mortero autonivelante es el mejoramiento de la base a recubrir, procurando una continuidad y uniformidad en todo su volumen. Este mortero puede ser usado tanto en interiores como exteriores.
Leveling mortars are used for various aspects of the construction sector, however, these are their most common uses:
- Projects that require anchoring bolts for machinery.
- Leveling base plates.
- Supporting machinery, columns, beams, and other structural elements.
- Repairing concrete, in structures affected by environmental agents, for example, saltpetre.
Main advantages of self-leveling mortar
En relación al variado uso de los morteros de nivelación, se produce a su vez unas ventajas constructivas considerables. Entre las tantas bondades hemos escogido a las siguientes como las más importantes:
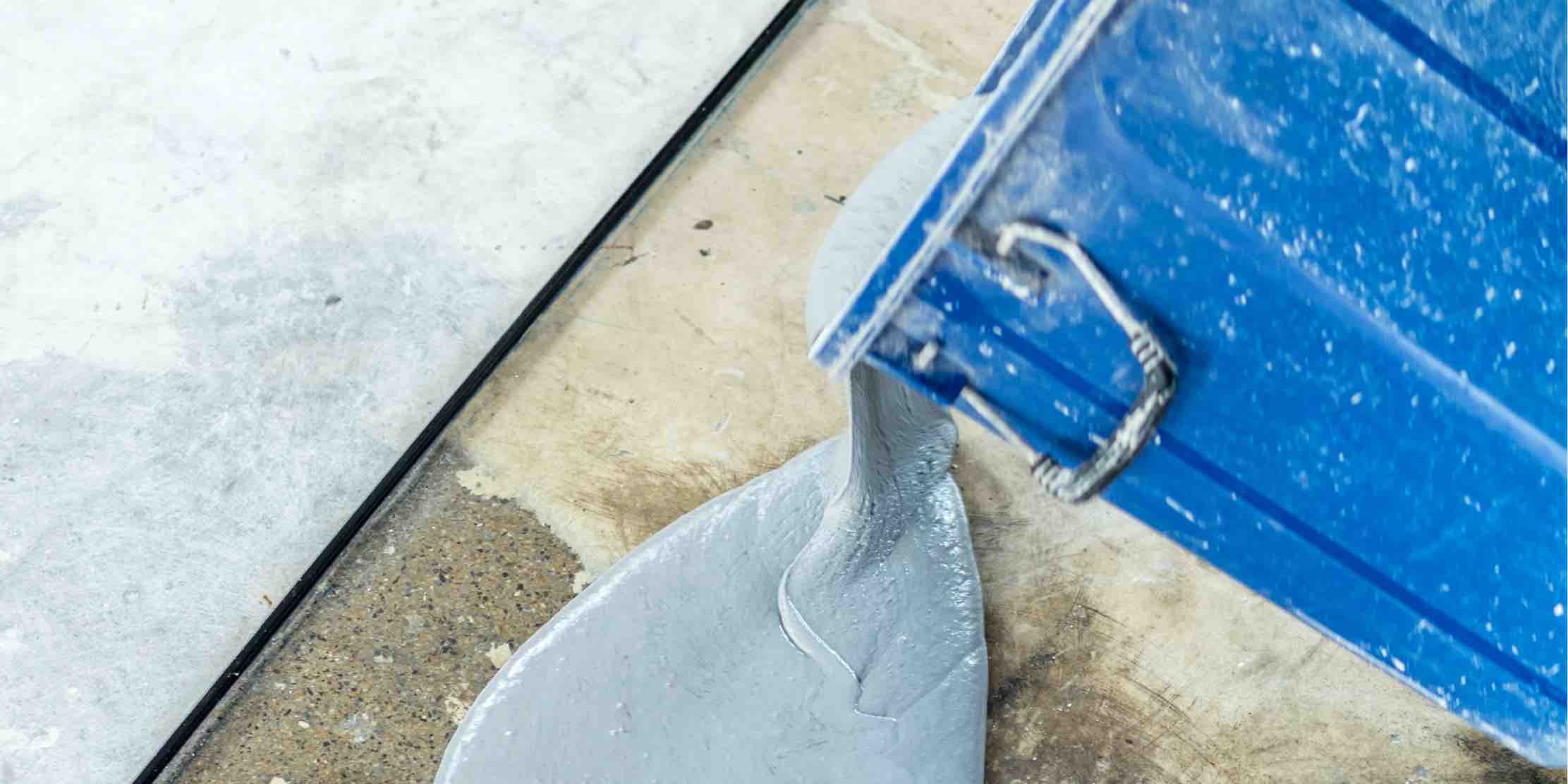
- It has a good adhesion capacity.
- High mechanical and abrasive resistance.
- It is an affordable option and has a positive financial impact since it reduces the coating execution time, the number of workers needed, and tools.
- It offers quality and excellent finishes, creating compact floors.
- It allows leveling large surfaces, thanks to its great fluidity.
- Its average drying time is 24 hours. However, the pavement can be used by traffic 4 hours after pouring it if the environmental conditions for setting are ideal.
- It can be used on a variety of surfaces (carpets, vinyl flooring, laminate flooring, and others) and environmental conditions.
- It is compatible with thermoacoustic insulation, and underfloor heating.
How to use self-leveling mortars?
Before proceeding how to pour these mortars, it is important to mention some preliminary points necessary to apply the coating correctly:
- The surface to be coated must be clean. It has to be healthy and free of oils, dust and any other substance that may hinder the adherence of the mortar.
- The surface must be exposed to water, but puddles must be avoided.
- If metal surfaces are to be coated, they will need to be thoroughly cleaned to remove any remaining grease, rust, paint and any other residual material.
- The surface must be hard and consistent.
- If the presence of any cracks, these must be repaired with special products.
- Expansion joints must be maintained.
To pour self-leveling mortars, these are the following steps:
- Kneading the mortar mixture, which should reach an approximately liquid state, but should also be a thick mixture. For this you can use pumping machines or a concrete mixer.
- Depending on the thickness of the applied coating, it is necessary to wait an equivalent number of days to carry out any finishes, such as tiling or waterproofing the mortar.
¿Qué es el hormigón autonivelante? ¿Existe?
Difícilmente te podemos dar una definición sobre él, porque la verdad es que no existe.
Hay mucha información en Internet acerca del hormigón autonivelante, pero es totalmente errónea, generando muchas incógnitas en los usuarios, porque en el mismo artículo te mezclan conceptos como hormigón y mortero tratándolo igual, cuando no es así.
No existe el hormigón autonivelante como material que tenga características, ventajas o composición propia para utilizarlo con fines específicos.
La gente lo confunde con mortero autonivelante, por lo que todo lo que has leído y encontrado aquí es totalmente veraz y se corresponde con la realidad.