How to polish concrete floor step by step:
- Preparation.
- Polishing.
- Sealing.
- Finishing.
Polished concrete has a modern and sophisticated appearance. Due to the polishing process, the performance of this construction material is improved significantly.
First, all imperfections need to be removed by grinding and polishing the surface until it is smooth. Finally the sealer is applied to minimise liquid absorption.
The process is simple to understand but requires time and physical effort.
Before you start reading the article and knowing how to polish a concrete floor, here are 2 other articles that may be of interest to you to increase your knowledge.
Let us help you decide. We are experts in polished concrete and industrial flooring.
What is concrete polishing?
Concrete polishing consists of using an abrasive composed of industrial diamonds on rough concrete surfaces to obtain a smooth floor finish.
Concrete can be polished dry or wet. At BECOSAN® we prefer to polish in wet conditions to reduce the amount of dust.
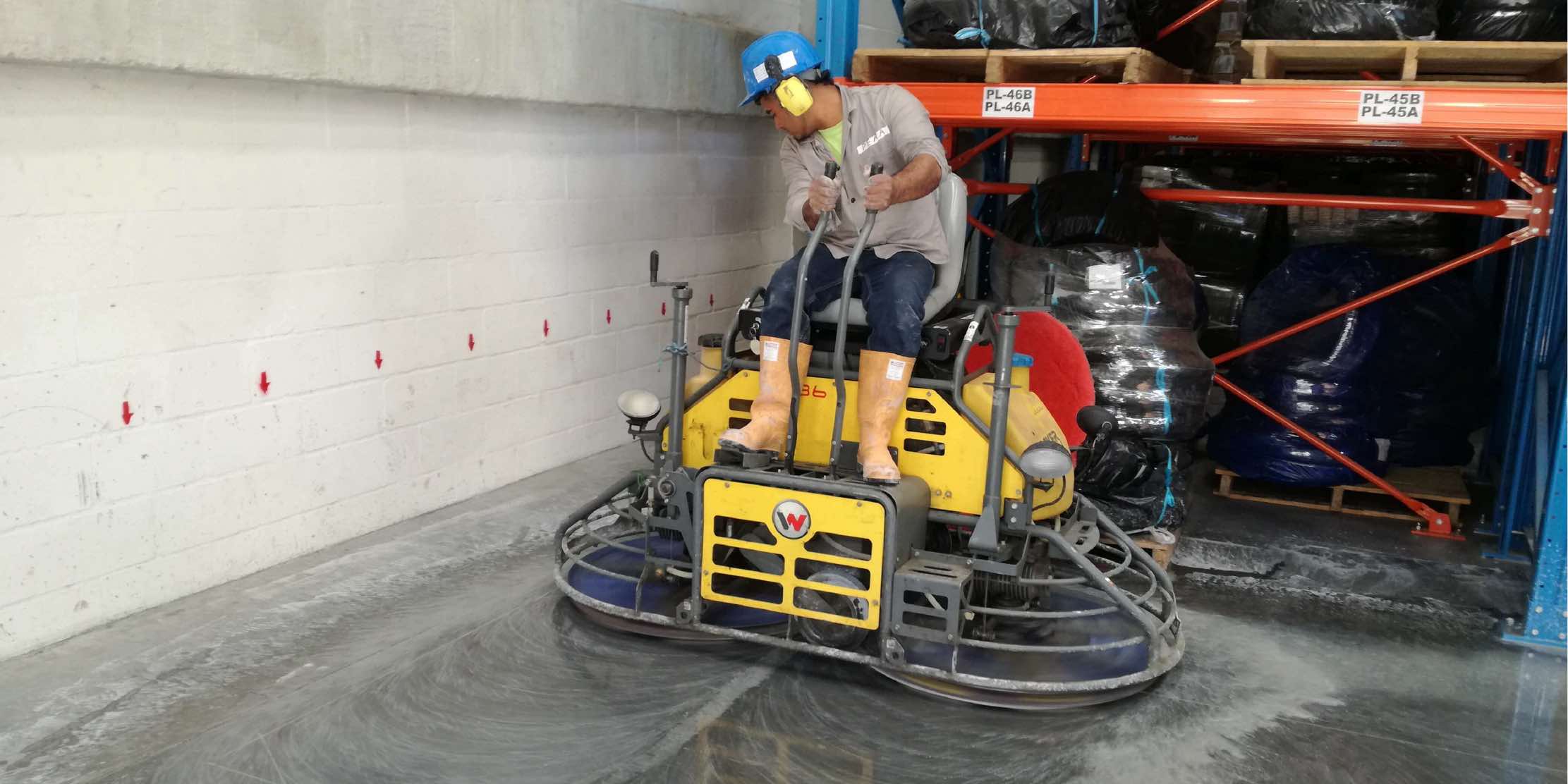
We can use two types of machines. The first is a traditional concrete polisher such as the HTC 800-4A 800mm, ideal for surface preparation. In addition, a power trowel, recommended for floor finishing, can also be used. The power trowel can be either manual, like the Honda GX150, or ride-on, like the Wacker CRT36-26A, a 36-inch double power trowel.
The polishing tool is a disc with an abrasive surface embedded with industrial diamonds. Industrial diamonds are commonly used in concrete polishing.
They are available in different strengths, shapes and sizes. The size of the industrial diamond is represented in terms of grit.
The size of the industrial diamond and the corresponding number of grits are inversely proportional to each other.
This means that discs with bigger diamonds have a smaller grit and vice versa.
The rougher the floor, the lower the grit. For the polishing of an industrial floor we use higher grits with smaller diamonds.
Therefore, in a traditional project, we start with a low grit number and will gradually increase it depending on the gloss level that the customer wants to achieve.
Why polish concrete?
A new concrete floor has a micro-rough surface. Before it can be used in an industrial or commercial environment, it must be smoothed and sealed.
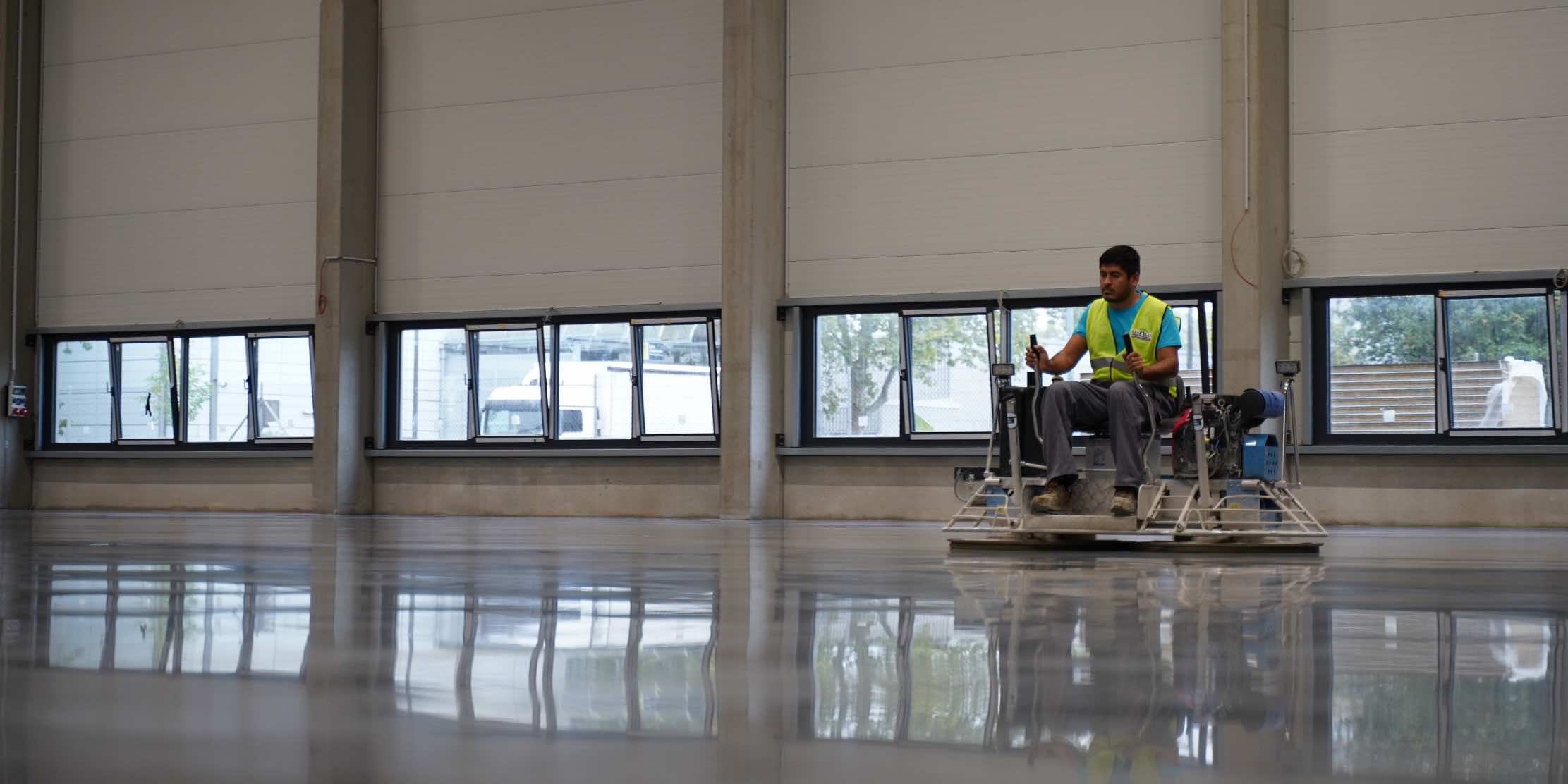
Perhaps most importantly, from our perspective, BECOSAN® needs to perform the polishing process before applying the BECOSAN® protective densifier and sealer, this being the last step in our process.
New concrete floors are the easiest to prepare – all we have to do is to allow the floor to cure. Normally, a well laid surface would take about 28 days to set.
A used floor is different. In an industrial environment or in a warehouse, a floor that has been used for a few years will be damaged. Bolts have been left anchored in the floor, several cracks have appeared and possibly some fluids have penetrated the surface. All this must be solved before polishing.
How to polish concrete floor?
Preparation of the concrete surface
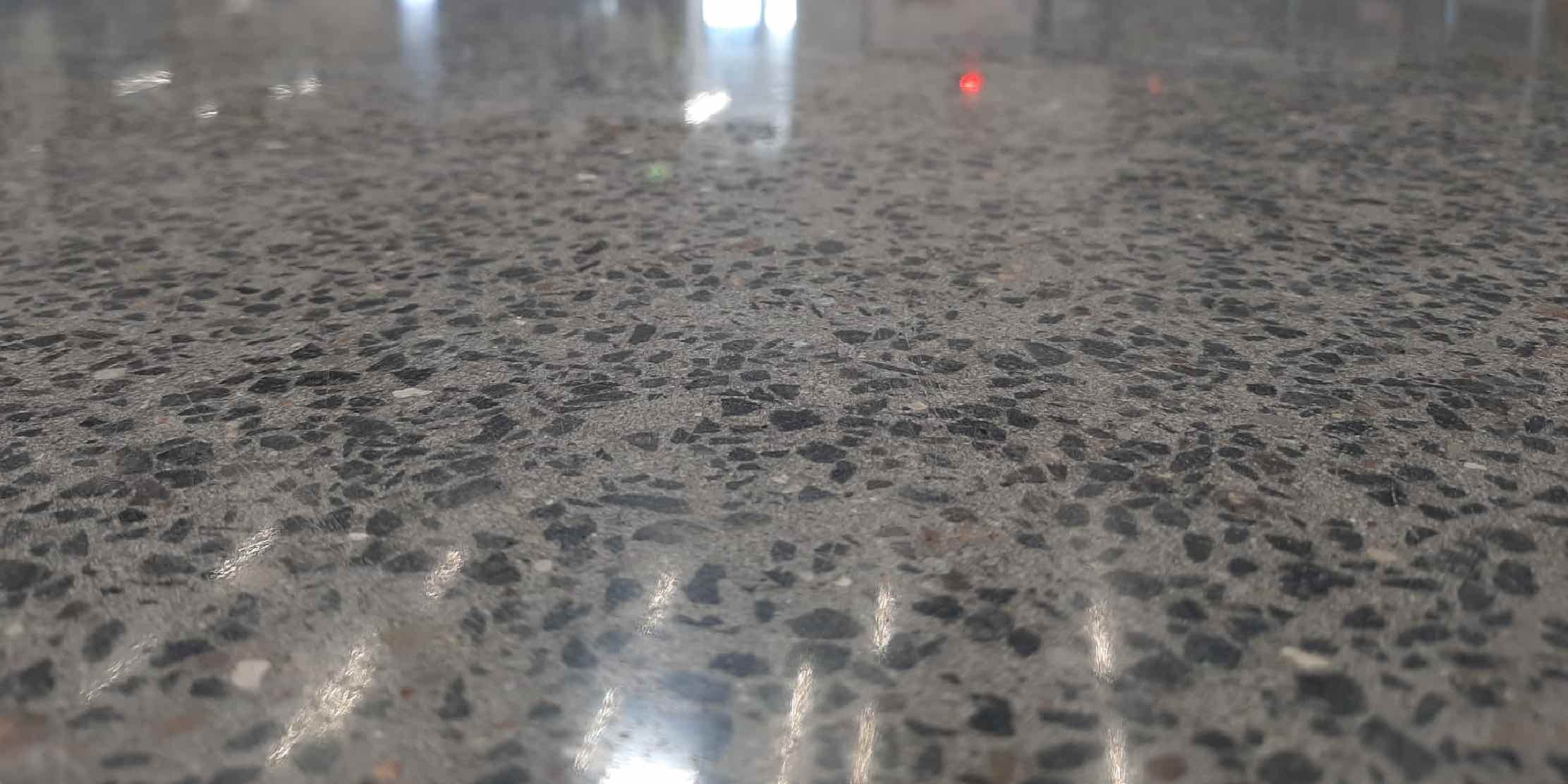
- Evaluating Concrete. For this, the Mohs’ test is recommended, which is used to determine the hardness of minerals (concrete). In this way we will be able to determine if it is a soft, medium or hard concrete and thus to adapt our polishing process.
- Use the tools provided in the kit to compare the hardness of concrete with the hardness of other minerals. The punch that is able to scratch the concrete, the lower number is the one that corresponds to the hardness of the floor.
- Use the tools provided in the kit to compare the hardness of concrete with the hardness of other minerals. The punch that is able to scratch the concrete, the lower number is the one that corresponds to the hardness of the floor.
- Clean the surface with an industrial scrubber and water. To remove difficult stains you can also add a solution of soap and water to the machine.
- For difficult stains or mildew, a stronger cleaner may be necessary. Hydrogen peroxide, ammonia, and phosphate cleaner (TSP) are good choices, but don’t mix these chemicals together. Choose and use only one chemical.
- Wear gloves and goggles before handling chemicals and keep the area ventilated.
- Repair cracks or flaws. It’s time to repair joints or floor damage.
- Use a special mortar for concrete cracks. Follow the manufacturer’s instructions to mix the mortar.
- Let the mortar dry completely before moving on to the next step.
Polishing concrete with coarse grit
- A concrete grinding machine is required. In addition, you must use specific abrasives to grind and polish the concrete floor.
- You can also choose to rent the necessary machinery. Keep in mind that this can be a considerable expense, depending on the size of the project. For small areas it is worth renting, but for large areas it is better to hire a POLISHED CONCRETE COMPANY or think about buying a machine.
- You can also choose to rent the necessary machinery. Keep in mind that this can be a considerable expense, depending on the size of the project. For small areas it is worth renting, but for large areas it is better to hire a POLISHED CONCRETE COMPANY or think about buying a machine.
- Wear protective clothing. Before handling the grinding machine, you should wear a dust mask, gloves, safety goggles and earplugs.
- Floor grinding is carried out dry. It is necessary to connect a vacuum cleaner to the grinding machine to avoid dust generation.
- While not strictly necessary, you can also wear a helmet to protect your head in case of an accident. This is especially important if you are working on a construction site.
- Wear safety shoes with a good grip to prevent accidents caused by slips.
- Polish the concrete with the coarsest disc. If the floor has many imperfections or difficult stains, start with grit 30, but if it is in good condition you can start the grinding process directly with grit 60.
- Keep in mind that these discs must contain industrial diamonds. If this is not the case, the result will not be as expected.
- Note that lower grits indicate coarser discs. In other words, grit 40 discs are coarser than grit 80 discs.
- Follow the instructions that come with your polisher to to attach the abrasives correctly. Run the machine over the entire concrete surface, working gradually from one corner to the diagonally opposite corner.
- Polish the concrete floor progressively, starting with the lowest grits and ending with the highest.
- The coarse of the required grits varies according to the hardness of the concrete. Surface preparation is usually done with grits 30, 60 and 80. However, resin abrasives of the grits 50, 100, 200, 400, 1000 and 3000 are used for polishing.
Concrete sealing and finishing
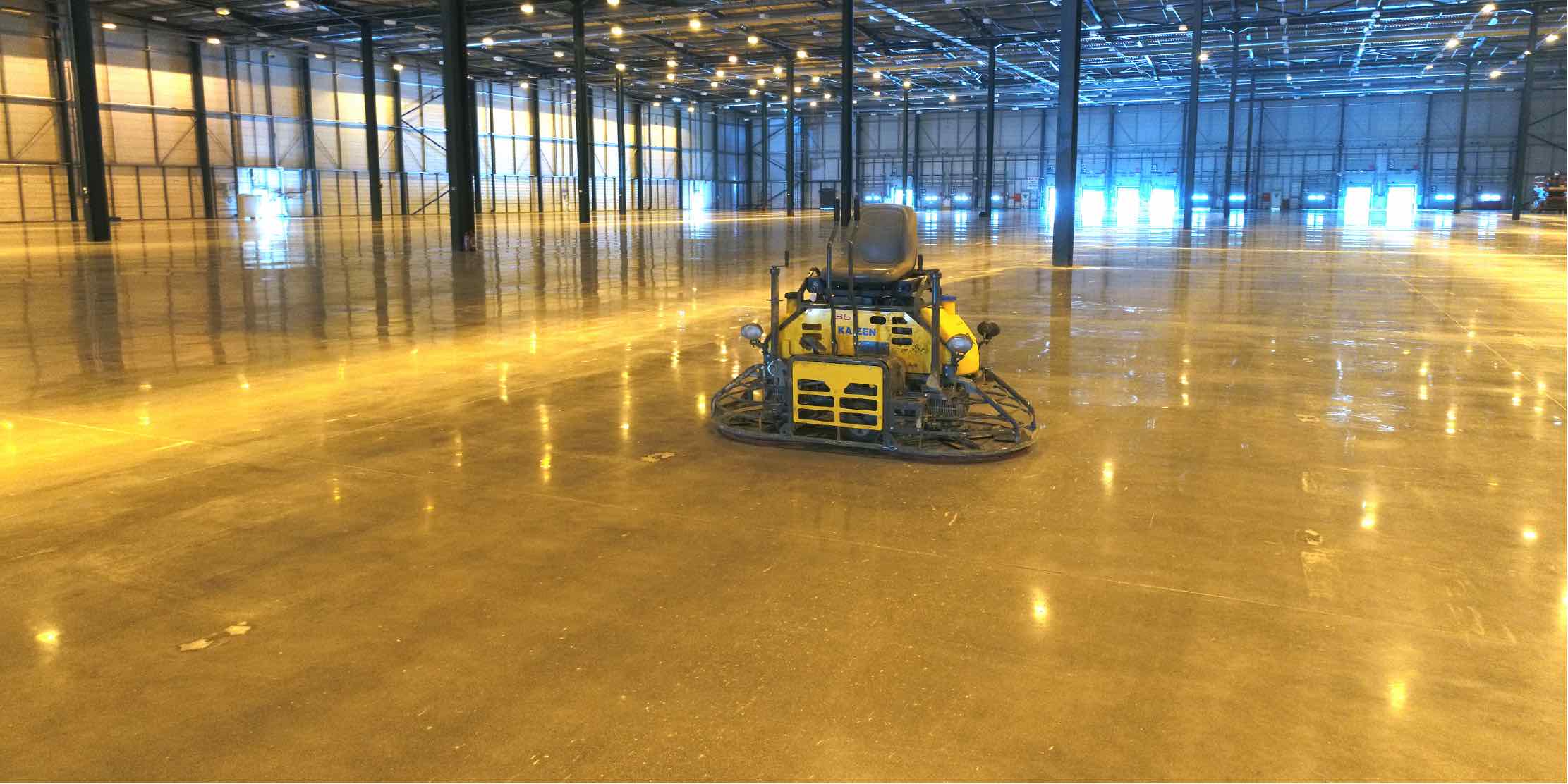
- Apply a thin layer of concrete sealer. Choose a water-based (solvent-free) CONCRETE SEALER and follow the manufacturer’s instructions. Normally these concrete sealers should be sprayed onto the surface.
- Our suggestion: BECOSAN® Protective Sealer
- Sealers protect concrete against grease, dirt and stains. In addition, the use of a sealer increases the gloss level of a polished concrete floor.
- The usual dosage of a concrete sealer is 0.1 litres per square meter or 100 ml per square meter.
- Apply in a single layer. It is important to distribute the sealer a micro-fiber mop, avoiding the formation of puddles. Wait between one and two hours for it to dry before proceeding with the next step.
- Polish the surface again with the finishing pads.;For this step you need a high speed burnisher and diamond pads. Work slowly and thoroughly, covering the entire surface at a steady pace.
- Move in the direction opposite to the direction in which you applied the sealer.
- Once finished, the floor will be smooth and glossy like glass.
- Wait at least 24 hours before using the floor. Wait for the sealer to dry completely before actively using the concrete floor.
- Drying time varies by manufacturer as well as ventilation and site conditions, but is generally between 24 and 48 hours.
- Once this period has elapsed, the polished floor is finished and ready for active use.
Dry or wet polishing?
There are two ways to polish: wet and dry. Dry polishing does not add water to the process and generates a lot of dust. To deal with this, a vacuum cleaner is connected to the grinding machine to aspirate the dust produced. All modern grinding machines are equipped with vacuum connections.
On a large scale, dry polishing is inconvenient. At BECOSAN® we always polish with a wet process. Water is poured on the floor, which is polished and grinded with a power trowel.
“Wet polishing is more efficient and keeps dust at ground level.”
Of course, polishing generates water slurry and cement dust that must be carefully removed.
Three types of finishing
At BECOSAN® we have three standard versions:
- Matt+
- Semi-Gloss
- High-Gloss.
Each finish involves several polishing steps using increasingly fine diamonds. After each phase, the floor must be cleaned with a scrubber dryer, such as the Gmatic Rotan 195 BT 125, which collects the sludge produced by the polishing and leaves the floor clean.
In the middle of the polishing process we apply our patented CONCRETE DENSIFIER which chemically reinforces the concrete surface.
At the end of the polishing process, we apply our impregnating sealer, which makes the floor more resistant to liquid absorption.
Finally, the floor is polished to achieve an attractive gloss finish.
In summary, the process for each finish can be described as follows:
- Matt+; grit 50, 100, densifier, grit 200, sealer.
- Semi-Gloss; grit 50, 100, densifier, grit 200, 400, sealer.
- High-Gloss; grit 50, 100, 200, densifier, grit 400, 1000, 3000, sealer.
Slurry removal
Concrete slurry is a toxic and highly alkaline substance that must be carefully removed. Often, the difference between a real concrete flooring professional and an irresponsible company is their commitment to slurry disposal.
“At BECOSAN® we take slurry disposal very seriously and use a three-step process.”
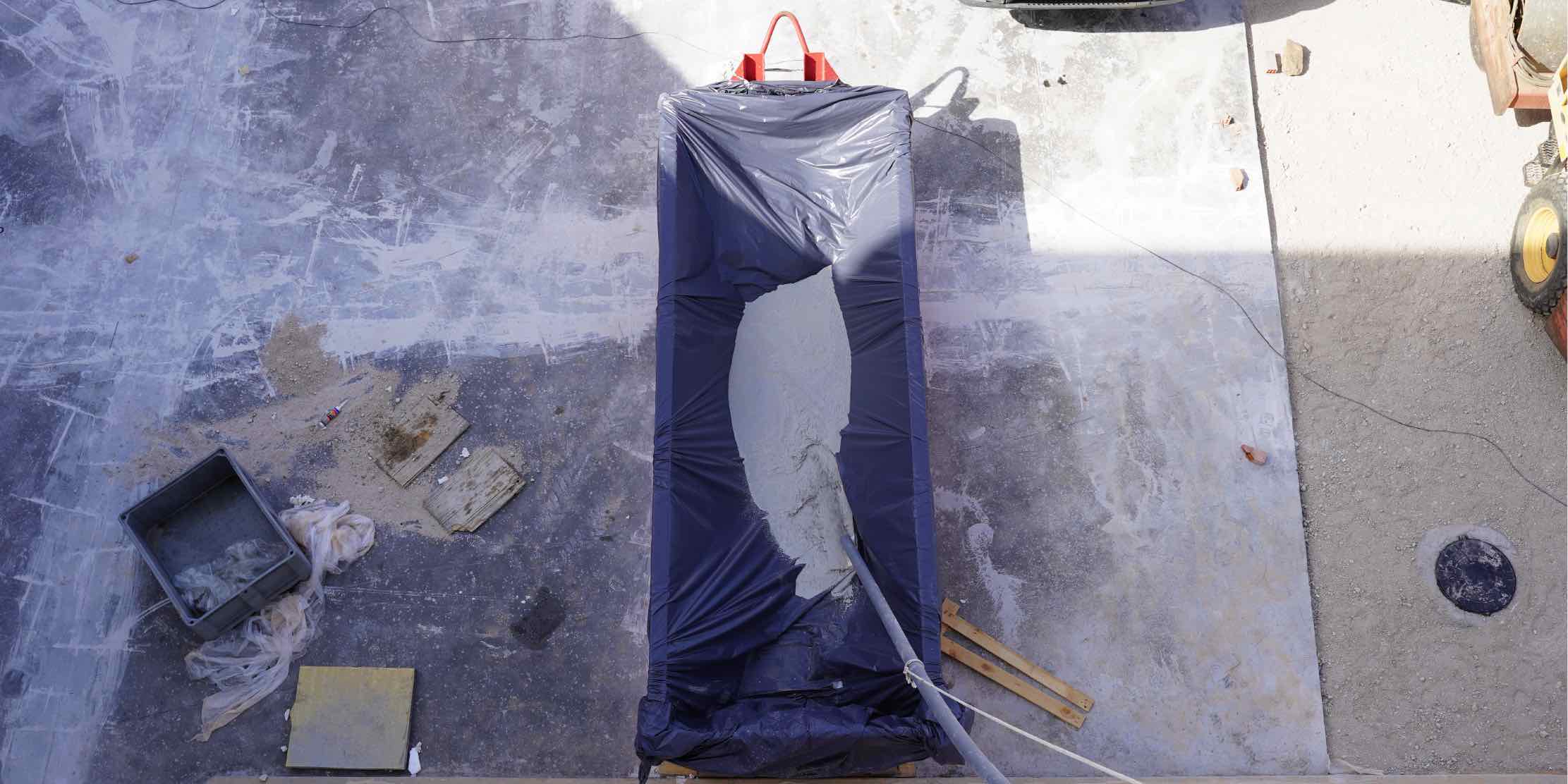
Separate and neutralize
The slurry is removed from the customer’s site and our BECOSAN® Separator is added to the mix. The separator transforms the PH value of a highly alkaline suspension to a PH-neutral value.
The separator also facilitates the separation of reusable clean water from the slurry, which can be safely discharged, while remaining a non-alkaline condensed slurry.
Solidify
Adding BECOSAN® Solidifier to the condensed slurry transforms it into a solid that can be moved and removed more easily.
Disposal
Solid waste can now be safely transported to a disposal point approved by local authorities.
How much does polished concrete cost?
A good question, but difficult to answer, as there are many factors that will affect the price.
- Quality.
- Damage.
- Size.
- Location.
Firstly, we must consider the QUALITY and, in particular, the hardness of the existing concrete.
Soft concrete is more difficult to polish, as there are many problems that can arise. The floor is rougher, which means that more abrasives will be used. Therefore, the surface would need a good preparation before a treatment with BECOSAN®.
We have to take into account the degree of DAMAGE to the concrete floor. How many bolts are anchored to the floor have to be removed? How many cracks have appeared? How much is the floor marked with paint and tyre marks?
In addition, we have to consider the SIZE of the floor. The larger and wider it is, the more efficient the polishing process can be.
Finally, the LOCATION of the pavement is important. Is it too far away? Is it easy to get in and out with machinery and slurry tanks? Are there authorized waste disposal sites nearby?
Considering the above, we estimate that in 2022 the cost of creating a world-class polished concrete floor with a long life span ranges from 6£ to 25£ per square meter.
You can find more information about each case here: polished concrete floor price.
We offer concrete polishing services in the UK and Europe.
10 years dust proof guarantee. Unique BECOSAN® patent
Polished concrete companies worldwide
Remember that if after this you want to contact a polished concrete company, we can help you. We have certified applicators all over the world.
BECOSAN® only works with certified applicators to ensure the quality of their finishes.
Contact us