The most commonly used synthetic materials for industrial floors, garages, logistics centres, and shopping malls are polyurethane and epoxy resin.
When naming these two types of synthetic floors there is often confusion, but these two types of flooring are very different and their polymeric nature differs considerably.
Some industrial sectors choose to use a polyurethane or epoxy floor, allowing continuous floors (without expansion joints), and because they offer a hygienic and waterproof finish.
Although usually, it’s a better option to install a polished concrete surface instead of a synthetic one.
What is a polyurethane floor?
A polyurethane floor is a concrete structure covered with thermoplastic polyurethane, which is a polymeric compound composed of hydroxy bases and diisocyanates.
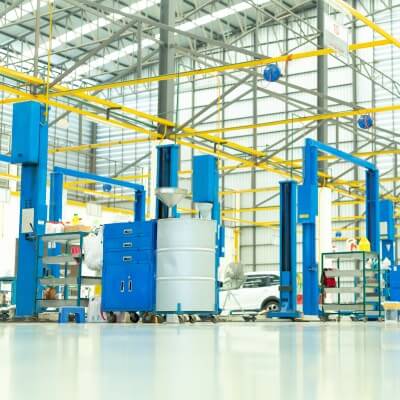
Polyurethane is added to the concrete floor’s surface creating an additional millimeter layer, which aims to protect the floor by reducing its porosity, making it waterproof and less vulnerable to the effects of temperature, ultraviolet radiation, and chemical attacks.
Another characteristic of a concrete floor covered with polyurethane is that it gains greater flexibility.
Technological improvements in the construction industry have managed to create a hybrid mix, consisting of cement and polyurethane, thus achieving that the entire structure has a synthetic part and not only on the surface.
Characteristics of a polyurethane floor
- Physical resistance to UV radiation, so the aesthetics of its finish are stable.
- It has great resistance to aggressive chemicals, such as acids, fats, oils, etc.
- Polyurethane floors and cement-polyurethane paving are structures with great flexibility and resistance to people and machinery traffic.
- Thermal resistance, especially at negative temperatures on the Celsius scale.
- Sensitivity to humidity and its alterations.
- It is susceptible to scratching caused by machinery traffic and pedestrian traffic.
- Easy to clean.
What is an epoxy floor?
Epoxy flooring is another type of concrete structure continuously covered by a synthetic material, which in this case is epoxy resin, also known technically as polyepoxide, a compound formed by a series of reactive polymers and prepolymers.
The most commonly used epoxy resin for coating concrete floors is a two-component product, which is made from the reaction between epichlorohydrin and bisphenol-A.
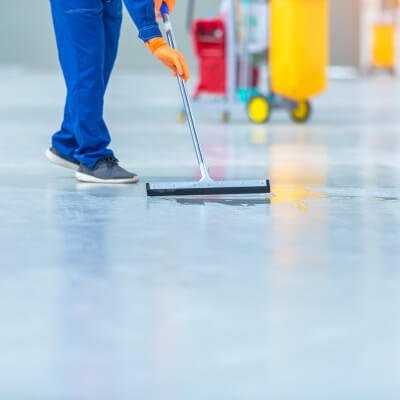
Being a bicomponent, the epoxy coating comprises 2 parts. In the first part, the mixture between the epoxy resin and the hardener reacts chemically, and in the second part, the coating hardens and adheres to the concrete floor.
Once the epoxy resin has completely adhered to the concrete floor, it provides greater mechanical resistance to abrasion caused by machinery and pedestrians, as well as an increase to its resistance to moisture and obtaining a better finish.
Characteristics of an epoxy floor
- High mechanical resistance to compression, impact, and scratches.
- Great adhesion to cover concrete surfaces.
- Resistance humidity changes.
- Reflective and shiny finish.
- Sensitive to thermal changes and freezing temperatures.
- Hard finish susceptible to sunlight, acids, fats, oils.
- Durable and easy to clean.
- Its installation is relatively complex and more expensive than polished concrete because it is necessary to consider various factors such as preparing the base on which it is to be applied on, humidity, substrate stability, among others.
Differences between a polyurethane floor and an epoxy floor
Depending on the subject, you can find many differences between epoxy floor and polyurethane flooring.
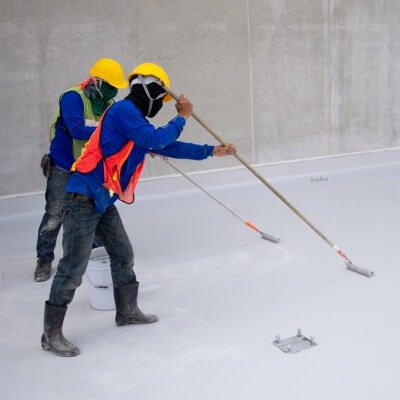
Chemical composition
The first difference would be that they have different chemical compositions.
Components
Analyzing their characteristics, we can find even more differences.
Whilst epoxy resin will always be a two-component product, the polyurethane can be either a two-component or one-component product.
Differentiated characteristics
Advantages of epoxy resin
Epoxy resin offers high levels of adhesion on any surface, providing a highly adhering coating that is also rigid and aesthetically appealing.
It also helps counteract the damaging effects of humidity.
Epoxy resin problems
On the other hand, epoxy floors are highly sensitive to most chemical and environment; mainly UV radiation and extreme temperatures.
Advantages of polyurethane
Polyurethane floors withstand the influence of UV rays and temperature changes, as well as to chemicals, maintaining the original aesthetics.
Polyurethane problems
However, when it comes to humidity, abrasion, impacts, and scratches, its resistance declines.
Summary:
Epoxy floors are the preferred option in terms of the mechanical resistance on concrete, but it reduces the structure’s elasticity and natural flexibility.
Whilst polyurethane provides the floor with more flexibility, at the expense of its mechanical resistance that may worsen with use.
What is the best synthetic coating for industrial floors?
There isn´t a single answer to this question. This will depend on the individual needs of each industry.
A type of concrete floor covering may be ideal for one specific industry, but it doesn’t have to be for another type of industry.
Due to their characteristics, polyurethane and epoxy resin floors are capable of meeting the demands of the food industry, since they offer a continuous, hygienic, and resistant surface.
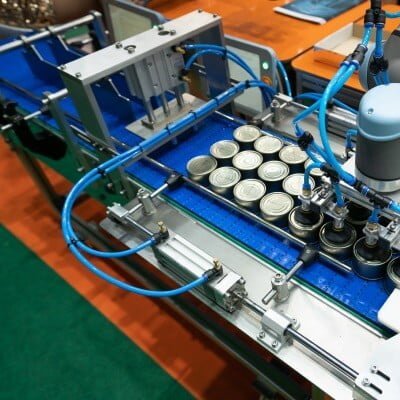
However, the metallurgical and chemical industry exclusively prefers polyurethane flooring, due to its high chemical and thermal resistance.
Epoxy floors are the preferred choice for the textile industry, as they comprise a non-slip, resistant, and waterproof surface, which simplifies cleaning tasks.
Alternative to resin floor coatings
An industrial warehouse concrete floor does not necessarily require a synthetic coating to be durable, waterproof and resistant, since other chemical treatments have been developed that improve the properties of a concrete floor.
Currently, one of the best treatments on the market is offered by the BECOSAN® system, which is a procedure that increases the concrete’s density by eliminating its porosity. This way, it is possible to obtain a floor with greater resistance and durability, without the need for coating it with a synthetic product.