Eine grundlegende Etappe für jedes zivile Bauprojekt, sei es häuslicher oder industrieller Natur, ist der Bau einer Betonplatte.
Dieser Prozess ist in den letzten Jahrzehnten stark modernisiert worden, wodurch die Qualität, Sicherheit und Effizienz, die bei Betonplatten erreicht werden kann, erhöht wurde. All dies führt zu äußerst widerstandsfähigen Belägen und Oberflächen, die sowohl Zuverlässigkeit und Sicherheit bieten.
Um diese Standards zu erreichen, ist es notwendig, dass der Bau und die Behandlung von Betonplatten strengen Qualitätskontrollen unterliegen, die mit immer polierten Geräten durchgeführt werden.
Nachfolgend werden die einzelnen Schritte beim Bau einer industriellen Betonplatte sowie einige der technischen Spezifikationen, die für ein einwandfreies Endergebnis erfüllt werden müssen, im Detail erläutert.
1. Die Vorbereitung des Bodens
Diese Phase besteht aus der Reinigung des Unterbodens des Bodenbelags, der Entfernung von Vegetation und aller Objekte, die den korrekten Prozess behindern und unterbrechen könnten.

Im industriellen Bereich ist es üblich, zur Beseitigung verbliebener Strukturen alter Gebäude auf Abbrucharbeiten zurückzugreifen. Alle Trümmer und Abfälle müssen an den jeweiligen Entlade- und Entsorgungsort transportiert werden.
Das Ziel all dieser Aktivitäten ist es, im Gelände eine gleichmäßige Beschaffenheit zu erzeugen und optimalen Eigenschaften für den Bau zu erhalten. Zu diesem Zweck werden Verbesserungsprozesse im Zusammenhang mit der Verdichtung des Unterbodens durch Verdichtung angewendet.
2. Platzierung des Metallgitters
Die Metallgitter bestehen aus Stahlstäben, die in Reihen und Spalten angeordnet sind. Die Stäbe werden durch Elektroschweißen verbunden oder mit dünnen Stäben oder Drähten abgebunden.

Das Metallgitter ist aufgrund seines Vorfertigungscharakters, der die Platzierung des Metallgitters erheblich vereinfacht, der am häufigsten verwendete Typ. Das Geflecht muss mit Hilfe von Metallstützen verankert werden, die sich auf dem Untergrund des Belags abstützen.
Ebenso gibt es Gelegenheiten, bei denen das Gitter weggelassen werden kann, da die Risse im Beton durch die Fugen eingedämmt werden. Dies ist jedoch nicht die ratsamste Lösung, da die Risse breiter werden können und so den Belag ernsthaft verschlechtern können.
3. Verlegung und Fertigstellung des Betons
Bevor der Beton gegossen wird, muss der Schalungsprozess durchgeführt werden.

Dabei handelt es sich um Formen, die die Abmessungen des Plattenabschnitts begrenzen. Sie können aus Metall, Kunststoff oder Holz sein.
Stahlbeton für Industrieplatten hier fügt in der Regel über Fasern (Metall und Kunststoff) in seiner konventionellen Zusammensetzung, basierend auf einer Mischung aus Kies, Sand, Wasser und Zement.
Die Kombination von Fasern mit Maschengewebe verbessert die Zugfestigkeit des Betons erheblich. Dieser Aspekt ermöglicht eine effektive Kontrolle von Betonabbindungsrissen, die durch plastisches Schwinden und thermische Kontraktion (oder Ausdehnung) verursacht werden.
Einbringen des Frischbetons
Der Beton muss zwischen Transport und Einbringen so wenig wie möglich gehandhabt werden. Damit soll eine Entmischung der Mischung und ein vorzeitiges Abbinden derselben vermieden werden. Aus diesem Grund wird der Einsatz von Mischfahrzeugen mit einem Entladekanal empfohlen.

Der Beton muss auf homogene Weise gegossen werden. Darüber hinaus muss der gegossene Beton mittels Vibration homogenisiert werden, um eingeschlossene Luft zu entfernen.
Ebenso ist die Temperatur ein wichtiger zu berücksichtigender Aspekt, da Temperaturen unter 5°C die Hydratation des Zements zunichte machen und die Agglomeration der Zuschlagstoffe im Beton beeinträchtigen.
Und unter heißen Bedingungen ist Beton anfällig für weitere Rissbildung, die als Folge der beschleunigten Verdampfung des in der Mischung enthaltenen Wassers auftritt.
Planieren und Verdichten
Sobald der Frischbeton über den gesamten Abschnitt der Platte verteilt ist und die entsprechende Dicke eingenommen hat, ist es an der Zeit, die Nivellierung vorzunehmen, um die Oberfläche zu regulieren und zu glätten.
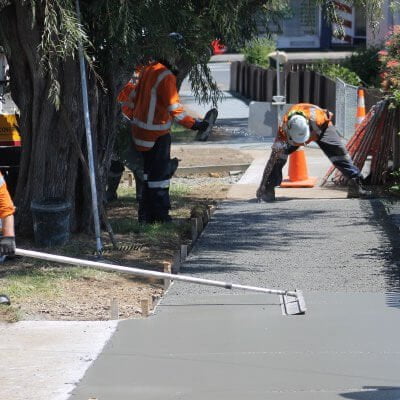
Zuvor wurde ein Aluminium-Schwingmaßstab verwendet. Heutzutage liegt jedoch der Laser-Nivellierer im Trend. Diese Maschine verwendet einen Lasersender, dessen Strahl von einem Kupferempfänger auf dem Nivellierfahrzeug empfangen wird.
Wenn das Nivelliergehäuse auf Unebenheiten im Beton stößt, lässt der Kupferempfänger es zur besseren Ausrichtung mit dem Laser aufwärts oder abwärts fahren.
Um jedoch eine größere Glätte auf der Oberfläche des Betons zu erzeugen, werden Instrumente zur Korrektur der Ebenheit eingesetzt, wie z.B. Schleiflinien (Stoßfräser und Prüf-Stab).
Das Nivellieren muss erfolgen, bevor der Beton zu bluten beginnt, d.h. bevor Wasser an der Oberfläche auftritt.
Glätten
Das Glätten ist eine Art der Endbearbeitung von Betonplatten, wodurch eine dichte, harte und glatte Oberfläche erzeugt wird.
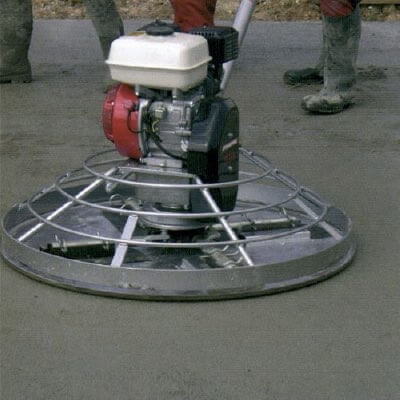
Dabei handelt es sich um ein mechanisches Verfahren, bei dem Straßenwalzen mit Schildern verwendet werden, die geneigt sein müssen, um die Kontaktfläche mit dem Beton zu verringern. Je steiler die Klingen sind, desto größer ist der Druck, so dass die Oberfläche glatter und dichter ist.
Das Glätten sollte systematisch und dann durchgeführt werden, wenn die überschüssige Feuchtigkeit verschwunden ist, d.h. wenn der Beton fast ausgehärtet ist.
Nach jedem Durchlauf der Walze ist es ratsam, die Neigung der Schaufeln zu erhöhen.
4. Fugen-Schnitt
Für diesen Vorgang werden Benzin- oder Elektroschneider mit Diamant- oder Schleifblättern verwendet.
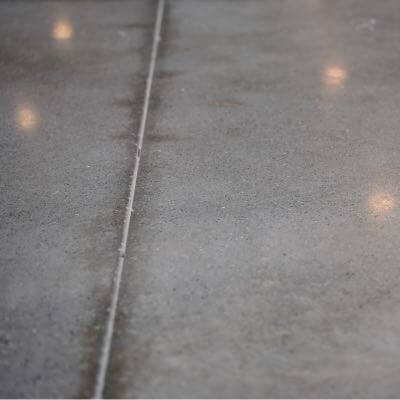
Es gibt zwei Schneidearten: konventionelles Nassschneiden und Trockenschneiden.
Das Trockenschneiden wird zur Herstellung der Dehnungsfugen im Beton verwendet. Diese Fugen werden hergestellt, wenn der polierte Beton noch nicht vollständig ausgehärtet ist. Damit soll die Rissbildung begrenzt werden.
Für dieses Verfahren werden Diamantblattfräser verwendet, die eine maximale Tiefe von 32 mm erreichen.
Der konventionelle Schnitt wird zwischen 4 und 12 Stunden nach Fertigstellung der Bramme durchgeführt; 4 Stunden in warmer Umgebung und 12 Stunden in kalter Umgebung. In diesem Fall beträgt die Schnitttiefe ein Drittel der Plattendicke.
Beide Arten von Schnitten müssen später versiegelt werden. Darüber hinaus müssen sie vor dem Aushärten des Betons hergestellt werden.
5. Aushärtung des Betons
Hierbei handelt es sich um die letzte Stufe beim Bau einer industriellen Betonplatte, deren Ziel es ist, die Hydratation des Zements zu verbessern und so die entsprechenden Feuchtigkeits- und Temperaturbedingungen im Beton zu erhalten. Die Aushärtung kann durch drei Methoden erfolgen.
- Aushärtende Massen: Mit diesen wird eine oberflächliche Versiegelung der Gehwegplatte durchgeführt.
- Polyethylen Folien: Mit der Verwendung dieser Art von synthetischen wasserdichten Papierfolien wird der Wasserverlust aus dem Beton minimiert.
- Nassbeschichtungen: Die Verwendung von Materialien wie Gewebe oder Materialien mit hoher Feuchtigkeitsspeicherung tragen dazu bei, den Feuchtigkeitsverlust des Betons zu minimieren.
6. Finale Betonoberfläche
In Abhängigkeit vom zu erhaltenden Boden und unter Berücksichtigung der Nutzung, auf die der Betonboden ausgerichtet ist, ist es manchmal zweckmäßig, ein kräftiges Polieren durchzuführen, welches dazu beiträgt, die Haltbarkeit und Abriebfestigkeit zu verbessern, den Wartungsaufwand zu verringern, das Auftreten von Staub zu eliminieren und andere Vorteile zu erzielen.
Die BECOSAN®-Behandlung trägt dazu bei, den Betonbelag auf neuen oder bereits abgenutzten Böden zu verdichten.