Una etapa fundamental para cualquier proyecto de construcción civil, es la construcción de una losa de hormigón.
Este proceso se ha modernizado enormemente en las últimas décadas, aumentando así los niveles de calidad, seguridad y eficiencia que pueden alcanzarse en losas de hormigón. Todo esto se traduce en pavimentos de gran resistencia y acabados tanto confiables como seguros.
Para lograr estos estándares, es necesario que la construcción y tratado de las losas de hormigón cumplan con rigurosos controles de calidad, los cuales se llevan a cabo con equipos cada vez más sofisticados.
A continuación vamos a detallar cuáles son las etapas de la construcción de una losa de hormigón industrial, así como algunas de las especificaciones técnicas con las que se deben cumplir para un resultado final adecuado.
1º Preparación del terreno
Esta etapa consiste en la limpieza del suelo base del pavimento, eliminando la vegetación y a cualquier objeto que pueda entorpecer e interrumpir la correcta construcción.

En el entorno industrial es común recurrir a demoliciones para eliminar estructuras remanentes de edificaciones antiguas. Todos los escombros y desperdicios han de ser transportados al respectivo lugar de descarga y desecho.
El objetivo de todas estas actividades es generar regularidad en el terreno y obtener las propiedades óptimas para la construcción. Para ello se aplican procesos de mejora relacionados con la densificación del suelo base, mediante la compactación.
2º Colocación de la red mallada
Los mallazos o red mallada están compuestos por barras de acero configurados en filas y columnas. Las barras están unidas por electrosoldaduras o atadas mediante barras finas o alambres.

El mallazo electrosoldado es el tipo más utilizado debido a su carácter de prefabricación, el cual simplifica considerablemente la colocación de la red metálica. La red mallada debe ser anclada mediante apoyos metálicos, sustentados en la sub-base del pavimento.
De la misma manera, existen ocasiones en las que el mallazo puede ser omitido, ya que las fisuras del hormigón son controladas por las juntas. No obstante, esto no es lo más recomendable, ya que las fisuras pueden incrementar su ancho, deteriorando así gravemente al pavimento.
3º Colocación y acabado del hormigón
Antes de proceder con el vertido del hormigón, es preciso realizar el proceso de encofrado.

Estos son moldes que delimitan las dimensiones de la sección de losa. Pueden ser metálicos, sintéticos, o de madera.
El hormigón armado de losas industriales suele presentar fibras (metálicas y sintéticas) en su composición convencional, basada en una mezcla de grava, arena, agua y cemento.
La combinación de fibras con mallazo mejora significativamente la resistencia del hormigón a la tracción. Este aspecto permite controlar efectivamente las fisuras del fraguado del concreto, las cuales son originadas por retracción plástica y contracción (o expansión) térmica.
Vertido del hormigón fresco
El hormigón ha de recibir la menor manipulación posible entre su transporte y su colocación. Con esto se busca evitar la segregación de la mezcla y un fraguado prematuro de la misma. Por ello, se recomienda el empleo de vehículos mezcladores que dispongan de un canal de descarga.

El vertido del hormigón debe presentar una distribución homogénea. Además, el hormigón vertido necesita ser homogenizado mediante vibrado para eliminar el aire ocluido.
De igual manera, la temperatura es un aspecto importante a considerar, ya que temperaturas inferiores a 5°C anulan la hidratación del cemento, perjudicando la aglomeración de agregados en el hormigón.
Y en condiciones calurosas, el hormigón es susceptible a un mayor agrietamiento, cuestión que sucede a raíz de una acelerada evaporación del agua presente en la mezcla.
Todo esto tendrá influencia en el tiempo que tarda el hormigón en secar.
Nivelación y compactación
Una vez el hormigón fresco ha sido distribuido por toda la sección de la losa, ocupando el espesor correspondiente, es momento de aplicar la nivelación para regular y suavizar la superficie.
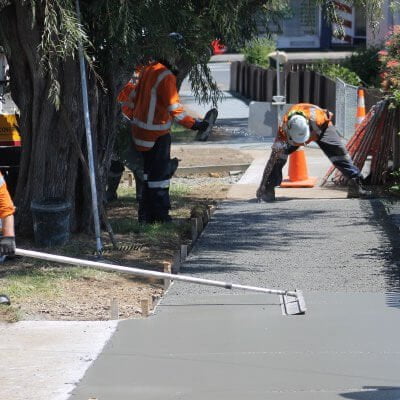
Anteriormente se hacía uso de una regla vibratoria de aluminio. Sin embargo, actualmente la niveladora láser es tendencia. Esta maquinaria hace uso de un emisor láser, cuyo rayo es recibido por un receptor de cobre en el vehículo nivelador.
A medida que el chasís nivelador se topa con desniveles en el hormigón, el receptor de cobre hace que suba o baje para obtener una mejor alineación con el láser.
No obstante, para generar una suavidad mayor en la superficie del hormigón se utilizan instrumentos de corrección de planicidad, como las reglas rectificadoras (bump cutter y check rod).
La nivelación debe hacerse antes de que el hormigón inicie su sangrado, es decir, antes de que el agua comience a surgir en la superficie.
Fratasado
El fratasado es un tipo de acabado de hormigón, el cual produce una superficie densa, dura y lisa.
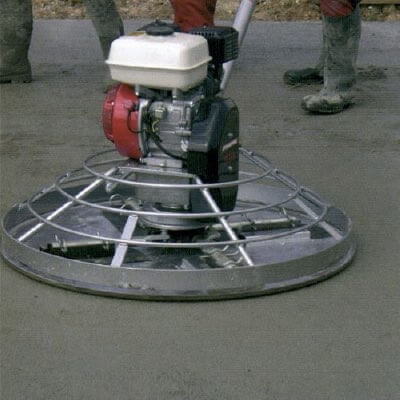
Éste consiste en un proceso mecánico que emplea aplanadoras con aspas, las cuales deben estar inclinadas para reducir el área de contacto con el hormigón. Mientras más inclinadas se encuentren las aspas mayor será la presión, por lo que la superficie será más lisa y densa.
El fratasado debe ejecutarse sistemáticamente y cuando el exceso de humedad haya desaparecido, es decir, cuando el hormigón esté más próximo al estado endurecido.
Después de cada pasada del aplanador es recomendable aumentar la inclinación de las aspas, además, debe hacerse el recorrido en dirección opuesta al anterior.
4º Corte de juntas
Para esta operación se utilizan cortadoras eléctricas o de gasolina, las cuales poseen discos abrasivos o de diamante.
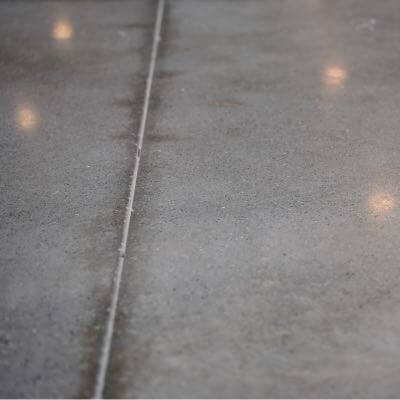
Existen dos tipos de corte: el corte convencional húmedo y el corte en seco.
El corte en seco se emplea para crear las juntas de dilatación en el hormigón. Estas juntas se realizan cuando el hormigón pulido aun no esta endurecido del todo. Con esto, se busca limitar el agrietamiento.
Para este proceso se emplean cortadoras con disco de diamante, obteniéndose una profundidad máxima de 32 mm.
El corte convencional se aplica entre 4 y 12 horas después del acabado de la losa; 4 horas en ambientes cálidos y 12 en ambientes fríos. En este caso, la profundidad del corte será un tercio del espesor de la losa.
Ambos tipos de cortes necesitan ser sellados posteriormente. Además, deben ser realizados antes de que el hormigón endurezca.
5º Curado del hormigón
Esta es la última etapa de la construcción de una losa de hormigón industrial, y su objetivo es mejorar la hidratación del cemento, conservando así las condiciones adecuadas de humedad y temperatura en el hormigón. El curado puede efectuarse mediante tres métodos.
- Compuestos de curado: por medio de estos, se realiza un sellado superficial de la losa de pavimento.
- Hojas de polietileno: con el uso de este tipo de hojas de papel impermeables de material sintético, se minimiza la pérdida de agua del concreto.
- Recubrimientos húmedos: El uso de materiales como telas o materiales con alta retención de humedad, ayudan a minimizar la pérdida de humedad del hormigón.
6º Acabado final del hormigón
A veces, dependiendo del suelo que se quiera obtener y teniendo en cuenta el uso al que esté enfocado el suelo de hormigón, conviene realizar un potente pulido de hormigón que ayudará a conseguir mejoras en la durabilidad, resistencia a la abrasión, reducir su mantenimiento, eliminar la aparición de polvo y otros beneficios.
El tratamiento BECOSAN® ayuda a densificar el pavimento de hormigón en suelos de nueva creación o ya gastado.