The phrase “Polished cement floor” can lead to confusion. From the customer’s point of view, this term can be misunderstood as a self-levelling mortar.
Furthermore, there are two other types of floor, which can also lead to confusion; microcement and polished concrete.
Similar doubts to the previous ones arise because the term can be interpreted in an ambiguous way.
In this short article, we want to explain what polished cement floors are and eliminate any doubts about one of the most important materials in the field of industrial construction.
What is polished cement?
Although the term “polished cement” suggests that the surface of the hydraulic binder particles has undergone a polishing process, this is in most part wrong.
Polished cement is a finish based on the composition as a mortar; in other words, it is comprised of sand, cement, water and a fraction of stone particles. After being placed as a coating over the paving, it then receives a polishing process.
Generally, polished cement is classified as an aesthetic coating, however, it is an additional layer that provides greater protection, durability, and resistance to traditional flooring.
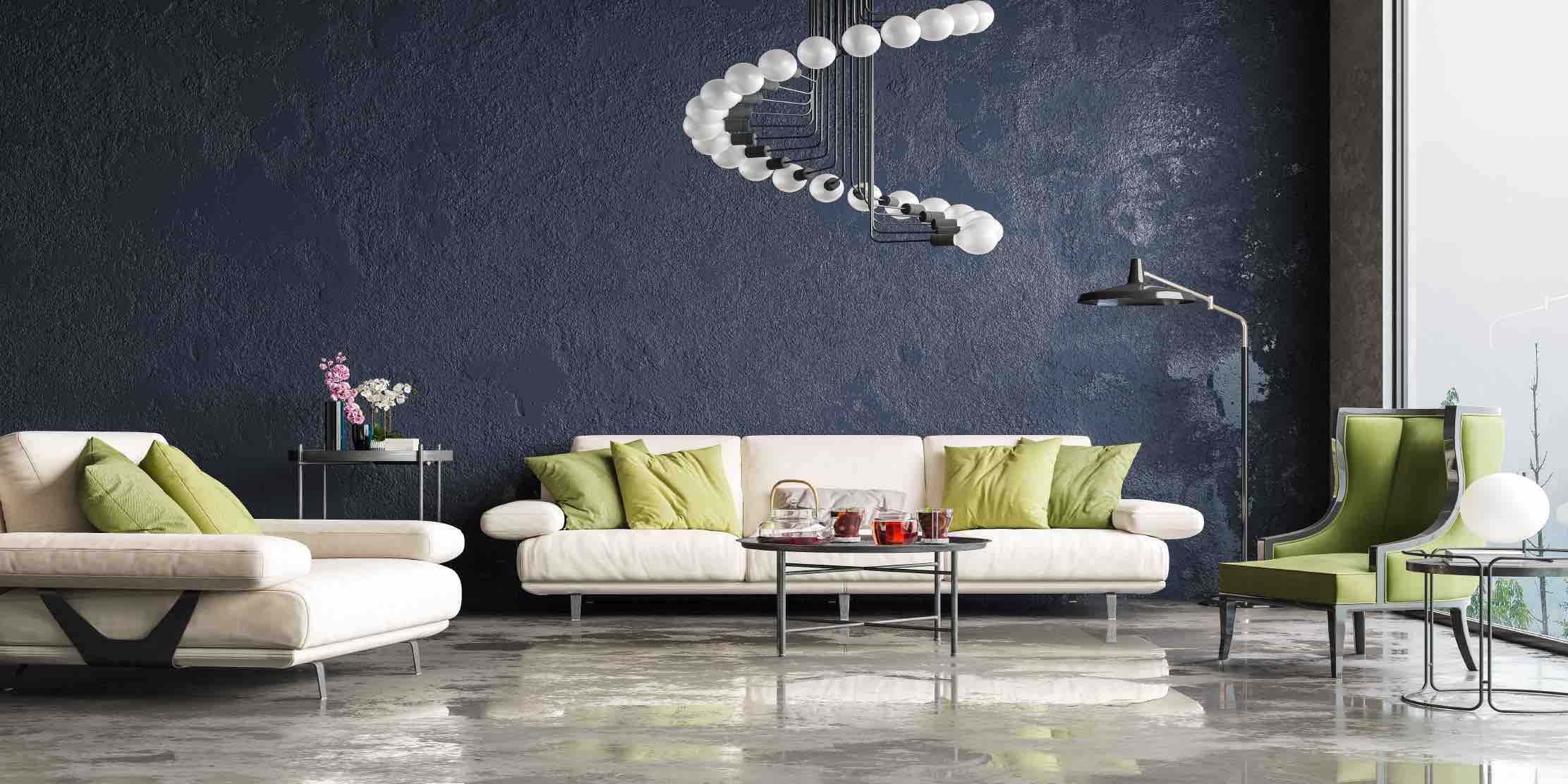
This finish needs to be polished to achieve aesthetic standards related to gloss and uniformity. However, another purpose for polishing the surface is to close the microscopic pores, making it impermeable.
Difference between polished cement and microcement
Polished cement and microcement are historically linked. This is because microcement was created to replace polished cement, producing greater aesthetics for surfaces and simplifying the pouring process, since, properly laid, micro-cement doesn’t need to be polished.
The most important differences between polished cement and microcement are the following:
- Regarding their composition, microcement is a mortar that contains, in addition to the conventional components, resins and quartz which provide a shine of its own to the coating’s mixture.
- In contrast to polished cement, microcement has particles that bind together into a dense cluster and divide when reacting to water, creating smaller particles.
- The minimum thickness of polished cement coatings is 5 centimeters, whilst the thickness of microcement finish is between 3 and 5 millimeters.
- Concrete floors with polished cement require joints. However, micro-cement allows for continuous, joint free surfaces..
Polished cement finishes are more useful in industrial environments, for both internal and external. Meanwhile, micro-cement finishes are ideal in internal domestic environments or any other that is undemanding and has a low-traffic.
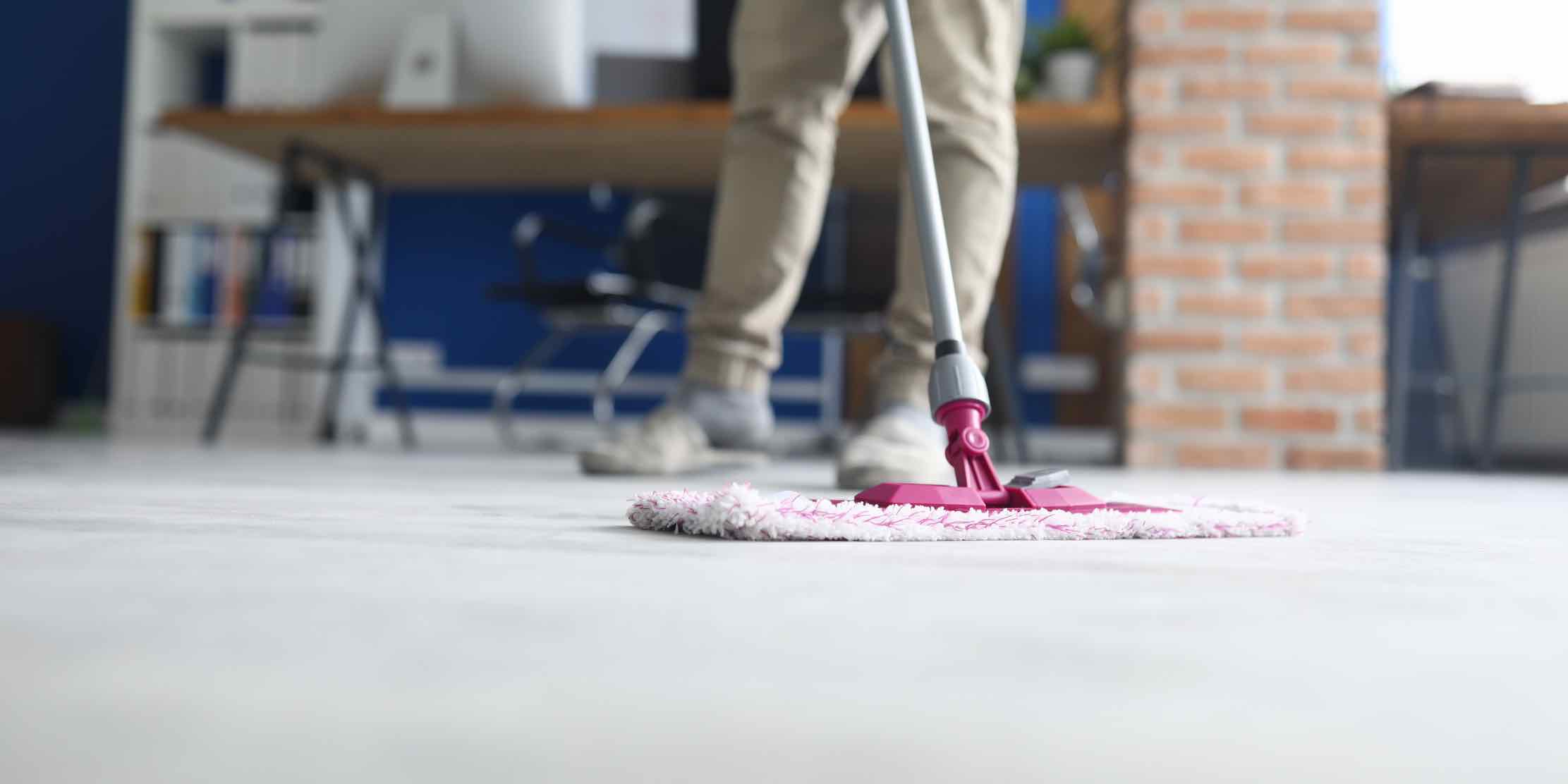
Advantages of polished cement
A concrete floor with polished cement meets the basic requirements of a traditional floor, adding new aspects that improve the behavior and performance of its surface.
Among the positive characteristics of a concrete floor with polished cement are:
- It’s relatively easy to apply.
- Their appearance.
- When installed correctly, it’s strong and durable.
- It’s an economical material for large surfaces.
- It helps cover any existing damage and unevenness.
- Colour can be personalized by applying dyes.
- It hardly needs maintenance.
Disadvantages of polished cement
- Low acoustic and thermal insulation.
- Sensitive to scratching (this does not occur with polished concrete).
- Shine is lost over time.
- Due to its high weight (120 km/m2), it’s not recommended to apply on raised floors.
- Joints are required, if not, cracks may appear.
Is polished cement floor the best option for an industrial surface?
The other possible confusion when it comes to polished cement is polished concrete.
Although a polished cement coating can be used in large industrial areas, the ideal solution is to use a polished concrete finish.
Polished concrete has unbeatable characteristics compared to polished cement. It offers a floor which is resistant to any activity, it’s cheap and easy to clean, it doesn’t slip and that is also attractive.
In industrial buildings and other industrial facilities, a polished concrete finish can even partially reduce electrical energy consumption, since the floor is capable of reflecting a good percentage of light.