Een industriële onderneming goed beheren is cruciaal en het is de belangrijkste manier om ervoor te zorgen dat de productieprocessen efficiënt verlopen.
Industrieel management maakt gebruik van verschillende technieken, maar ook van de kennis en innovatie van professionals om de productiviteit en orde in een onderneming te optimaliseren.
[toc]
Een industriële onderneming kan niet functioneren zonder management, aangezien dit zou leiden tot een niet-productieve chaos die geleidelijk aan de hele industrie zou ruïneren.
Waarom is het beheer van een industriële onderneming zo belangrijk?
Eerst en vooral is industrieel management belangrijk omdat het inspanningen, vaardigheden en hulpmiddelen omzet in productiviteit en efficiëntie.
Industrieel management bestaat uit een waaier aan technieken die erop gericht zijn om tijd, kosten en verlies te minimaliseren en de productiewaarde te verhogen.
Hoewel het beheer over het algemeen wordt geassocieerd met het productieproces van de industriële faciliteiten, vallen ook processen zoals opslag, organisatie en distributie onder industrieel management, aangezien deze bedrijfsactiviteiten nauw verwant zijn met productie.
Het moet worden opgemerkt dat industrieel management belangrijk is voor het plannen van renovatie- en/of onderhoudswerken van het industrieel magazijn, zodat de productieprocessen niet onderbroken of negatief beïnvloed worden.
Wie is er verantwoordelijk voor het beheer van industriële ruimtes?
In productie zijn industrieel ingenieurs de voornaamste managers, aangezien zij de kennis, ervaring en professionele training hebben om de technieken correct toe te passen.

Een industrieel ingenieur is vertrouwd met productieprocessen. Hij/zij is immers een deskundige die is opgeleid om te streven naar industriële optimalisatie.
Het zijn echter vaak de bedrijfsleiders die verantwoordelijk zijn voor het management van een industriële onderneming.
Een manager moet naast de productie ook andere activiteiten organiseren, plannen en controleren, zoals opslag, distributie, enz.
Technieken om efficiënt een industriële onderneming te beheren
Momenteel zijn er heel veel verschillende efficiënte industriële managementtechnieken, sommige met een eerder traditionele aanpak en andere met een modernere en innovatievere invalshoek.
Moderne technieken verschillen van traditionele technieken in het feit dat ze geen lineaire manier van denken hebben, maar uitgaan van een dynamischere en flexibelere manier om complexe activiteiten te begrijpen.
Van alle industriële managementtechnieken, zijn dit de belangrijkste:
5S-methode
Dit is een Japanse managementtechniek, die bestaat uit een set van 5 stappen gebaseerd op oosterse principes. De naam verwijst naar het feit dat elk van de 5 woorden begint met de letter S.

De verschillende stappen van de 5S-methode zijn:
- Scheiden: deze fase bestaat uit het identificeren en scheiden van noodzakelijke items voor de productie en items die nutteloos en onnodig zijn.
- Sorteren: deze fase gaat over orde en bestaat in principe uit het indelen van industriële ruimtes, en het opstellen van de benodigde items voor een optimale productie.
- Schoonmaken: deze fase houdt verband met de netheid en de hygiëne van de industriële ruimte.
- Systematiseren: dit is een fase waarin onregelmatigheden, zoals rommel en vuil, worden voorkomen en de juiste regels en procedures voor productie worden vastgesteld.
- Standhouden: deze laatste fase gaat over discipline, de fase waarin het belangrijk is om zich te blijven inspannen en de productieprocessen te blijven verbeteren.
Kaizen
Dit is een andere oosterse managementtechniek, met een filosofische toets. Het woord Kaizen betekent verbetering.
Het belangrijkste doel van deze managementfilosofie is om de industriële kwaliteit te optimaliseren door middel van een permanent verbeteringsproces dat bestaat uit eenvoudige, specifieke acties.
Deze techniek beschouwt de industrie als een geheel, waarbij elk onderdeel (werknemers, managers, ingenieurs, bestuurders, enz.) een actieve rol speelt in het streven naar voortdurende verbetering.
Totaal productief onderhoud (TPM)
Dit is een andere Japanse managementfilosofie. Deze techniek is erop gericht om tijdsverlies (storingen, onderbrekingen, stilstand, enz.), , kwaliteitsverlies en kosten tijdens het productieproces te minimaliseren.
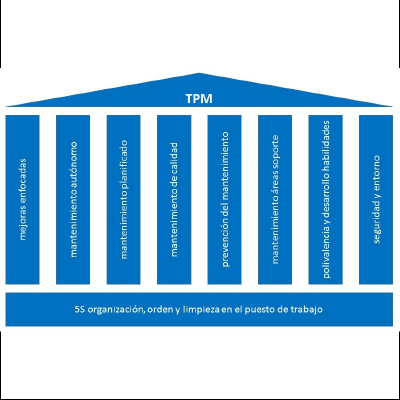
- Gerichte verbeteringen: het is een proces van voortdurende verbetering dat de basis bepaalt om de nodige veranderingen op een geplande en precieze manier te kunnen doorvoeren.
- Autonoom onderhoud: een reeks activiteiten uitgevoerd door operatoren om machines en apparatuur te onderhouden en klaar te maken voor gebruik.
- Gepland onderhoud: systematische activiteiten die worden uitgevoerd om machines en apparatuur in slechte staat te herstellen.
- Initiële controle: bestaat uit het ontdekken van mogelijke storingen om de slijtage van apparatuur en machines te beperken en de onderhoudskosten te verlagen.
- Kwaliteitsonderhoud: nadruk op de naleving van de regelgeving en de kwaliteitsnormen.
- Opleiding: proces van opleiding en begeleiding van het personeel in hun respectievelijke vakgebieden.
- Totaal productief onderhoud in kantoren: dit verwijst naar het doorvoeren van de hele reeks industriële verbeteringen in de kantooromgeving.
- Veiligheid en milieu: de naleving van de door de overheid opgelegde milieu- en veiligheidswetten.
8D
De 8D-methode bestaat uit 8 fasen, gericht op probleemoplossing. Deze managementtechniek wordt vooral gebruikt om problemen bij kwaliteitscontroles aan te pakken.

De 8 fasen van deze methode zijn:
- Een team van experts samenstellen met kennis in verschillende vakgebieden.
- Het probleem precies beschrijven.
- Het probleem tijdelijk oplossen.
- De oorzaak van het probleem zoeken.
- Verschillende oplossingen vaststellen en onderzoeken.
- De definitieve oplossing implementeren.
- Het ontstaan van soortgelijke problemen in de toekomst voorkomen.
- De inspanning van het team belonen.